Choosing the Right Distillation Kits for Your Needs |
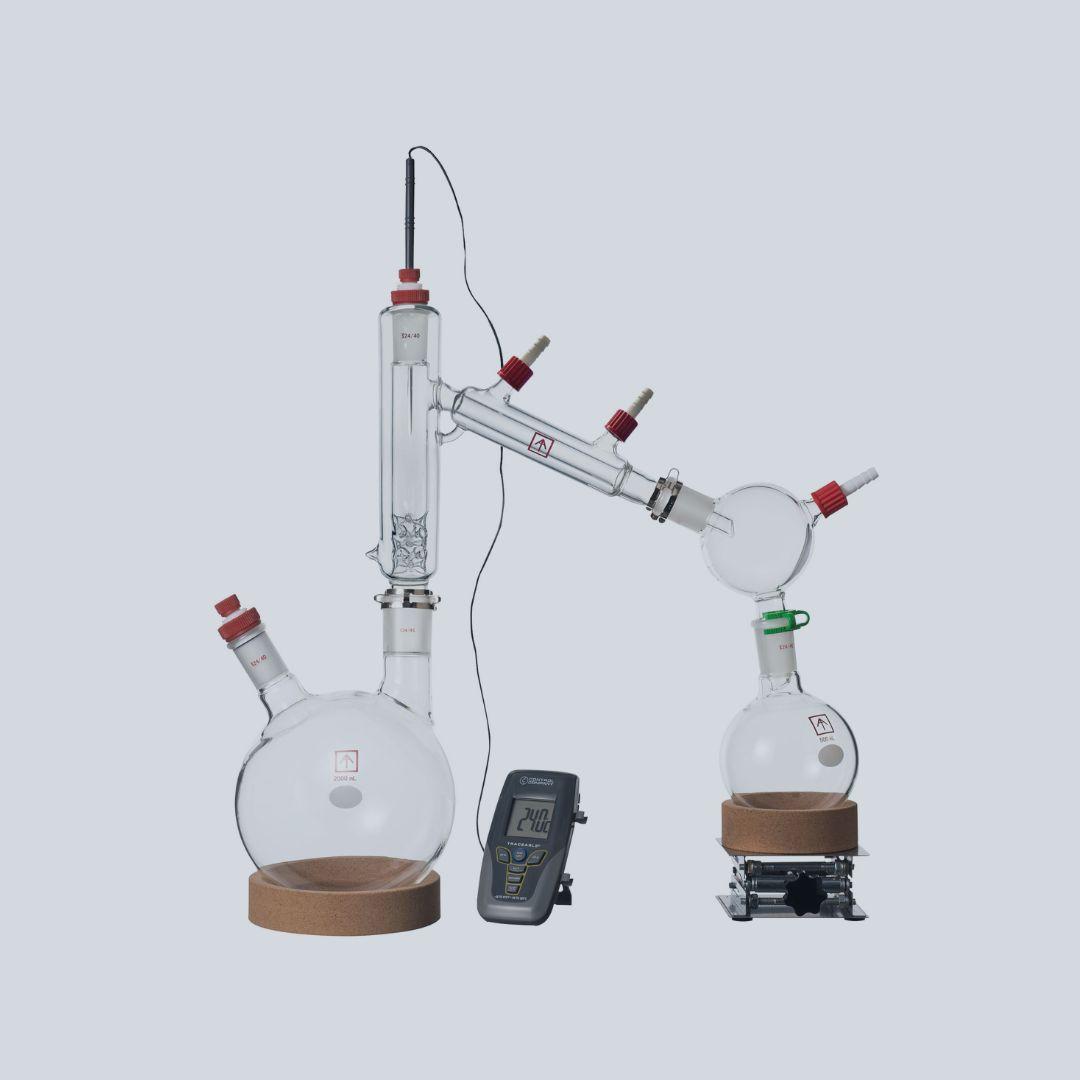
What Is Distillation?
Distillation is a process of separating the components or substances from a mixture. In chemistry, it is used to separate liquids from nonvolatile solids or two or more liquids with different boiling points. This technique is also applied in a variety of industrial and laboratory processes.[1]
Distillation can be conducted in various methods. Read this complete distillation kit buying guide to help you make an informed decision for your specific requirements.
Different Distillation Methods
1. Simple Distillation
Simple distillation is a method of separating components of a liquid mixture based on differences in their boiling points. This process is called “simple” because it involves only a single distillation step.
The principle behind simple distillation is based on the fact that different substances in a mixture have different boiling points. This specific method is only used if the difference in boiling point between two components is greater than 100 °C (212 °F).[2]
This method is used to distil various substances, such as vegetable oils, liquid samples, solvents, and water. [3]
2. Fractional Distillation
Fractional distillation is used to separate miscible, volatile liquids of similar or close boiling points. It requires the use of a fractionating column apparatus to simulate the separation. [3]
While it uses the same apparatus as simple distillation, the partial condensation of the vapour in fractional distillation occurs in a separate component called a fractionating column. Within the column, the rising vapour interacts with the condensing vapour, which causes the enrichment of the vapour with the more volatile component.
This method is used in various industrial applications, the most common of which is in the distillation of crude oil.
3. Vacuum Distillation
Vacuum distillation refers to the process of separating mixtures with high boiling points under reduced pressure.
Vacuum distillation is based on the principle that a reduced pressure decreases the boiling point of compounds. This method follows this principle specifically when the boiling point of the desired compound is difficult to achieve or will cause the mixture to decompose.
4. Stream Distillation
This refers to a special type of technique used to separate temperature-sensitive components of a mixture.
Most complex organic compounds do not dissolve in water. Steam distillation operates on the principle that heating a mixture of two or more immiscible liquids increases the system’s vapour pressure, which enables the purification of organic compounds at temperatures below their decomposition points.
5. Azeotropic Distillation
It is a specialised type of separating the components of an azeotropic mixture. An azeotropic mixture refers to two or more liquids that cannot be separated by normal distillation because the vapours formed during the boiling process contain almost the same ratio of constituents as the original mixture. [6]
Azeotropic distillation involves the addition of a third component, such as entrainer, the solvent, or the mass separating agent (MSA) to alter the composition of the vapour phase, allowing for the separation of the original components.
Azeotropic distillation is used in various industries such as polymer, chemical, agrochemical, and pharmaceutical industries.
6. Reactive Distillation
Reactive distillation is a hybrid process that combines chemical reaction and distillation in a single apparatus. When a solid catalyst is used in the operation, it can also be called a catalytic distillation.
The principle of reactive distillation involves the simultaneous occurrence of a chemical reaction and the separation of elements within a distillation column, which provides a valuable synergistic effect that overcomes the equilibrium limitations of many reactions.
7. Hydrodistillation
Hydrodistillation has been a longstanding practice that involves the use of water or steam to vaporise the volatile compounds present in the plant material, which are then condensed and collected as essential oils.
The core aspect of this process is the use of water in either its liquid or vapour form which can carry volatile compounds from plant materials without causing thermal degradation.
8. Molecular Distillation
Molecular distillation is a type of short-path distillation conducted under low-pressure vacuum conditions. This method is employed for the purification, concentration, and separation of common natural products, particularly those that are thermally sensitive. [9]
The principle of molecular distillation relies on the separation of various substances, which is driven by differences in their volatility. This separation occurs when a substance reaches its boiling point. [10]
This distillation technique can be applied in different nourishment production processes. Some of its applications include the obtainment of amide, extraction of omega-3 fatty acids, paraffin wax, and monoglycerides, and production of lactic acid.
9. Rotary Evaporation
Rotary evaporation is the method of decreasing the volume of a solvent by spreading it inside a vessel at elevated temperature and reduced pressure. This process facilitates the swift removal of excess solvent, particularly from samples with lower volatility. [11]
The working principle of a rotary evaporator is based on the fact that the boiling point of liquids decreases with reduced pressure. By lowering the pressure, the solvent can vaporise at lower temperatures compared to boiling in a normal atmosphere. [12]
Rotary evaporation is commonly employed when separating low-boiling solvents like ethyl acetate or n-hexane from compounds that exist in solid form at room temperature.
10. Flash Distillation
Also known as equilibrium distillation, this technique refers to a single-stage continuous operation in which a liquid mixture undergoes partial vaporisation. [13]
Flash distillation uses vaporisation to separate the compounds. Molecules with low boiling points condense and those with high boiling points remain in the vapour phase, which gradually results in saturation. Further condensation occurs at the bottom, allowing vapours to condense, while liquids descend and are collected at the bottom. [14]
This technique is used in various applications, such as refinement of crude oil and desalination of ocean water.
Which Distillation Method Should You Use?
To help you determine the right distillation technique, here are some key aspects you should consider:
- Identify the key components in the distillation process as well as the physical and chemical properties of the mixture. Learn about their boiling points, chemical reactivity, and heat sensitivity.
- Choose a method that aligns with the scale of your operation. Different techniques are suitable for laboratory-scale experiments, pilot-scale processes, or large-scale industrial applications.
- Consider the energy requirements and environmental impact of the distillation technique.
- Choose a technique that aligns with the available resources and expertise of the personnel involved.
- Consult experts in the field to gather information on the most suitable distillation techniques for your specific needs.
Different Types of Distillation Kits:
1. Simple Distillation Kit
- Burner
- Distilling Flask
- Thermometer
- Condenser
- Receiving Flask
Flash distillation uses vaporisation to separate the compounds. Molecules with low boiling points condense and those with high boiling points remain in the vapour phase, which gradually results in saturation. Further condensation occurs at the bottom, allowing vapours to condense, while liquids descend and are collected at the bottom. [14]
2. Fractional Distillation Kit
Fractionating Column
- Burner
- Condenser
- Thermometer
- Round-Bottom Flask
Receiving Flask
- Purification of liquids
- Oil refineries and chemical plants
- Separation of liquefied air
- Production of high-quality silicon, which is used in semiconductors
3. Vacuum Distillation Kit
Heat
- Reaction Vessel
- Fractionating Column
- Reflux
- Cold Trap
- Cooling
- Distillate
- Receiver
Vacuum Unit
Acquiring pure compounds in chemical and pharmaceutical processes
Distillation of crude oil
4. Steam Distillation Kit
Distillation Flask
- Condenser
- Receiving Flask
- Florentine Vase
- Heat
Glass Column
- Manufacturing of essential oils and perfumes
- Production of consumer food products
- Petroleum industry
5. Azeotropic Distillation Kit
Heat
- Round-Bottom Flask
- Thermometer
- Erlenmeyer
- Burette
- Reflux Condenser
Entrainer
Product purification
Purification of allyl alcohol, butenal, tetrahydrofuran solvents
6. Reactive Distillation Kit
Heating Bath
- Drain Valve
- Vessel
- Stirrer
- Motor
- Condenser
- Reflux Divider
- Product Cooler
- Vacuum
- First & Final Receivers
Vent
- Distillation of chemicals limited by chemical equilibrium
7. Hydro-distillation Kit
Heater
- Water Condenser
- Connecter
- Separating Funnel
- Distiller
- Thermometer
Receiving Flasks
Extraction of essential oils from plant materials
Distillation of heat-sensitive components
8. Molecular Distillation Kit
Feeding System
- Short-Path Evaporator With Internal Condenser
- Receiving System
- Cold Trap
Controller Console
- Fat extraction
- Carotene extraction
- Purification of natural essential oils
- Amide obtainment
- Purification of capsaicin
9. Rotary Evaporation Kit
Rotary Motor
- Vacuum Source
- Glass Tube
- Heating Bath
- Condenser
Receiving Flask
Handling of heat-sensitive procedures in medical and biological fields
- Trapping hazardous waste liquids
- Mixing reactants
- Flavour extractions
- Sample preparations
Solvent removal, separation, and recycling
Rotary Motor
- Vacuum Source
- Glass Tube
- Heating Bath
- Condenser
Receiving Flask
- Production of high-purity substances in pharmaceutical and chemical industries
11. Kugelrohr Distillation Kit
Kugelrohr (Ball Tube)
- Kugelrohr Flasks
- Heating System
- Receiving Flask
Cooling Bath
- Purification of small quantities of high-boiling-point compounds
12. Microscale Distillation Kit
Sand Bath
- Spin Vane/Boiling Stone
- Hickman Head
- Clamp
Water Condenser
Distillation of small amounts of substances in laboratory settings
Educational purposes and research laboratories
How to Choose the Right Distillery Equipment?
Material Compatibility in Distillation
Consider the materials used in the distillation kit. It should be compatible with the substances being distilled to avoid chemical reactions or contamination.
Distillation Kit Scale and Capacity
The scale and capacity of the distillation kit must properly accommodate the mixture to be processed. Larger-scale industrial processes may require specialised equipment, while smaller-scale operations in laboratory settings may benefit from more compact setups. Your chosen equipment should efficiently handle the intended workload to optimise productivity.
Temperature Control in Distillation
In distillation processes, accurate temperature control is essential to achieve effective separation and prevent thermal degradation. The distillation kit should have precise temperature control settings, such as digital temperature controllers or reflux ratio adjustments to ensure that the desired temperatures are maintained throughout the process.
Ease of Operation and Maintenance
A user-friendly distillation equipment simplifies the operation and maintenance processes, making it accessible to both novice users and experienced professionals. Look for features such as intuitive controls, easy assembly, and straightforward maintenance procedures. This enhances overall efficiency and reduces the likelihood of operational errors.
Safety Considerations
Safety is paramount in distillation processes due to the potential for exposure to high temperatures, pressure, and volatile substances. Look for safety features in distillation kits, including pressure relief valves, emergency shut-off mechanisms, and secure sealing systems to minimise risks and ensure a safe working environment.
Cost-Effectiveness
While it's important to stay within budget constraints, prioritising quality and performance ensures a reliable and efficient distillation process over time. For cost-effective distillation solutions, consider factors such as the durability of materials, safety features, and long-term maintenance costs.
Optimise Your Lab With State-Of-The-Art Distillation Kits
Selecting the right distillation kit is a crucial step in achieving an efficient, safe, and successful distillation process. Understanding the properties of the substances you’re working on and recognising the scale of your operation are all pivotal aspects in making an informed distillation kit selection.
Explore industry-recommended distilled equipment from Across International. Our range of distillation equipment is designed to meet the highest laboratory standards with precision and reliability. Browse our selection now.